Fraunhofer stellt innovative flexible Folie auf PLA-Basis vor
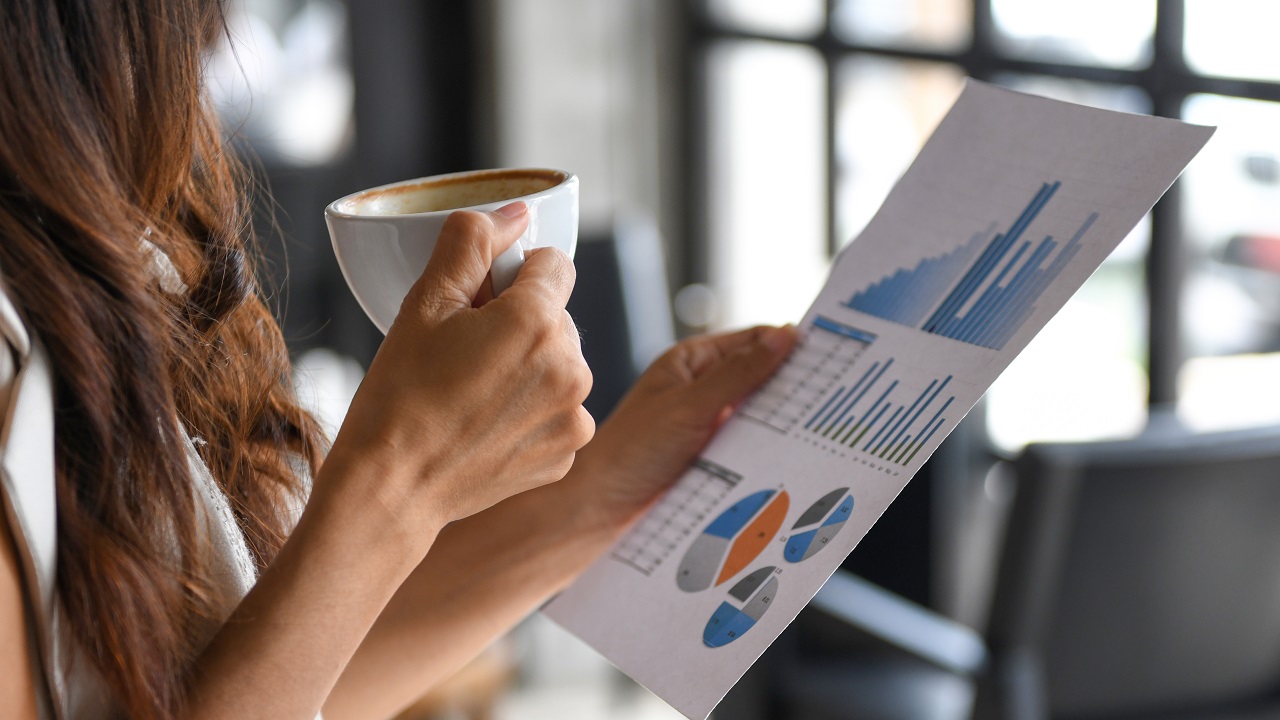
Flexible Einweg-Kunststofffolien, die häufig in Einkaufs- und Müllsäcken zu finden sind, werden überwiegend aus erdölgewonnenem Polyethylen niedriger Dichte (LDPE) hergestellt. Diese Folien haben einen erheblichen CO2-Fußabdruck und tragen zur Umweltverschmutzung bei. Ein Team des Fraunhofer-Instituts für Angewandte Polymerforschung IAP hat nun ein flexibles und recycelbares Kunststofffolienmaterial auf Basis des Biokunststoffs Polylactid (PLA) entwickelt und damit den Weg für dessen Kommerzialisierung geebnet. Als Anerkennung für ihre Bemühungen werden sie mit dem Joseph-von-Fraunhofer-Preis 2024 ausgezeichnet.
Recycling und Defossilisierung sind für nachhaltige Kunststoffe unerlässlich. Im Idealfall werden Kunststoffe nach Gebrauch in ihre Grundbestandteile zerlegt und dann zur Herstellung neuer Kunststoffe mit den gleichen Eigenschaften verwendet. Im Kreislauf von Produktion, Nutzung und Wiederverwendung geht jedoch einiges an Material verloren. “ Um die Kreislaufwirtschaft weiter zu fördern, müssen diese Verluste durch nicht-fossile Rohstoffe ausgeglichen werden. Das ist eine Herausforderung, da biobasierte Äquivalente für fossile Kunststoffe mit den gleichen Eigenschaften in der Regel nicht verfügbar sind«, erklärt Dr. Antje Lieske, Leiterin der Abteilung Polymersynthese am Fraunhofer IAP im Potsdam Science Park. “ Lieske weist weiter darauf hin, dass verschiedene Additive diese Eigenschaften zwar verbessern können, aber Recyclingprozesse stören, hohe Kosten verursachen können, Umweltrisiken darstellen und vor allem nicht aus biobasierten Quellen stammen.
Polylactid (PLA), ein Biopolyester, bietet eine vielversprechende Lösung für dieses Problem: Es ist biobasiert, biologisch abbaubar, leicht recycelbar und verfügt über ein erhebliches Marktpotenzial unter den Biokunststoffen. Seine hohe Steifigkeit macht es ideal für starre Verpackungen wie Einwegbecher, aber es war nicht für flexible Einwegverpackungen wie Einkaufstüten geeignet, die eine Hauptquelle für Kunststoffabfälle sind. Dr. Antje Lieske hat sich gemeinsam mit ihren Kollegen André Gomoll und Dr. Benjamín Rodríguez vom Fraunhofer IAP dieser Herausforderung gestellt.
„Wir haben Weichmacher, sogenannte Polyether, direkt in die Polymerkette integriert, um die Flexibilität des Materials langfristig zu erhöhen“, erklärt Dr. Benjamín Rodríguez. „Polyether sind im Handel erhältlich, ungiftig und können aus biobasierten Rohstoffen hergestellt werden. Früher wurden dem PLA Weichmacher als separate Additive zugesetzt, aber mit der Zeit wanderten diese Moleküle heraus, wodurch das PLA wieder steif und starr wurde. Um dies zu verhindern, verankerten wir den Polyether am Polymer. Wir haben PLA-basierte Blockcopolymere synthetisiert, bei denen das Polyetherkettensegment an beiden Enden kovalent mit PLA-Kettensegmenten verbunden ist.“
Das Ergebnis ist ein innovatives, flexibles PLA-Material, das frei von migrierenden Weichmachern ist und im Gegensatz zu LDPE zu mindestens 80 Prozent aus biobasiertem Material besteht. „Langfristig könnten wir diesen Anteil auf fast 100 Prozent steigern“, erklärt Gomoll. „Darüber hinaus kann unser Material durch einen einfachen Syntheseprozess kostengünstig aus kommerziell verfügbaren Rohstoffen hergestellt werden. Dieser Prozess kann von mittelständischen Unternehmen vor Ort als kontinuierlicher Betrieb durchgeführt werden, ohne dass große Syntheseanlagen erforderlich sind. Bisher konnte PLA nur in Großanlagen rentabel hergestellt werden, wobei kleinere Unternehmen von der Herstellung ausgeschlossen wurden. Darüber hinaus kann das neue PLA-Material mit herkömmlichen Anlagen ähnlich wie LDPE zu Kunststofffolien verarbeitet und mit deutlich geringerem Energieaufwand als LDPE chemisch recycelt werden“, ergänzt Gomoll.
Diese besonderen Materialeigenschaften veranlassten das Unternehmen der Polymer-Gruppe, das Produkt zu kommerzialisieren. Im Jahr 2023 hat die SoBiCo GmbH, ein Tochterunternehmen der Polymer-Gruppe, eine Produktionsanlage für die neuen PLA-Blockcopolymere in Pferdsfeld, Westdeutschland, in Betrieb genommen. Die Anlage produziert derzeit jährlich 2.000 Tonnen des neuen Biokunststoffs unter dem Markennamen Plactid®. Langfristig soll die Produktion auf bis zu 10.000 Tonnen des flexiblen PLA-Materials pro Jahr skaliert werden.
Diese neue Klasse von Biokunststoffen wird die Nachhaltigkeit von Kunststoffverpackungsmaterialien erheblich verbessern. Über flexible Verpackungsfolien hinaus hat das innovative Material das Potenzial, ganz neue Anwendungen zu erschließen, etwa im Automobilbereich, in der Textilindustrie und in der additiven Fertigung.